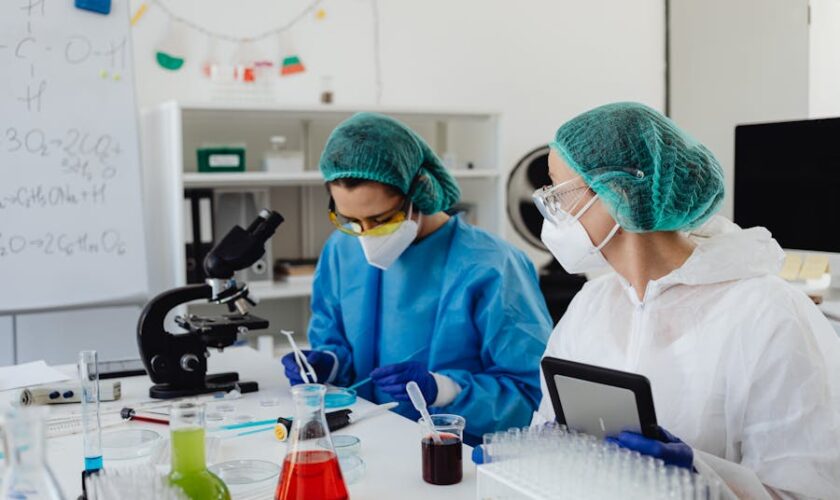
Here’s Why You Should Never Take a Haphazard Approach to Workplace Hazards
In business, trial and error isn’t always a bad thing. This is how you develop your products, after all, or settle on that eye-catching ad campaign that changes everything. If you aren’t willing to fail, then let’s be honest, you probably won’t succeed.
But, a haphazard approach isn’t always best, especially when it comes to workplace hazards like dangerous chemicals or equipment. In this instance, taking risks can prove fatal to your company, and potentially your team.
This is especially true in areas like healthcare and construction jobs, where hazards are ever-present. In this article, we’ll consider just a few of the risks that can come from assuming safety in these environments is something you can get right ‘later on’.
# 1 – The Cost of Inappropriate Facilities
When you’re building business facilities, you may be tempted to rush the process along by assuming you can make that space safe later. Unfortunately, that’s rarely wise, especially if you’re dealing in something like laboratory construction where you’ll need to consider integrated safety features like fume hoods and ample HVAC systems.
Luckily from a safety perspective, a laboratory missing these key things is unlikely to ever receive the all-clear. Unfortunately adding crucial hazard-reducing elements will cost a lot more, and take far longer, in a space that’s already been designed without.
By incorporating all hazard precautions at the planning stage, you can save yourself all of that hassle, ensuring a lab or factory that’s fully equipped to keep your team and business safe from day one.
# 2 – The ‘Too Little, Too Late’ Conundrum
Providing compensation or improving your processes after a worker receives an injury can feel like a gesture that offers too little and comes too late. That’s because safety, especially where hazards are concerned, should be dealt with proactively, rather than reactively. If you wait to see what harm hazards do before taking action, then you’ve already failed in your duty.
It’s far better to take ample time understanding the risks you face, and ensuring priorities like certain safety procedures upfront. This can highlight things like the need for additional training long before staff knowledge gaps become a problem. That way, you can avoid accidents, and keep your team running as well as it possibly can.
# 3 – Your Reputation Will Never Recover
Notable workplace accidents or fatalities tend to make the headlines in a major way, especially if neglectful processes like the improper handling of known hazards are in play. This can lead to reputational damage that proves devastating, even if you improve your processes as a result. That’s true regardless of whether you seek dedicated reputation management, especially if an incident involved employee fatalities.
By comparison, proactive, well-prepared, and compliant hazard processes, which you implement from your earliest efforts, can provide the groundwork for a great reputation as a trusted, caring employer and brand.
Working with hazardous materials is never easy, but it’ll be a lot easier if you avoid these risks of a haphazard approach.